In the ever-evolving landscape of construction materials, TMT (Thermo-Mechanically Treated) steel bars have undergone a remarkable transformation over the years. From their humble beginnings to the adoption of advanced manufacturing techniques, the evolution of TMT bars has revolutionized the construction industry. Join us as we delve into the fascinating journey of TMT steel bars from traditional to advanced manufacturing methods.
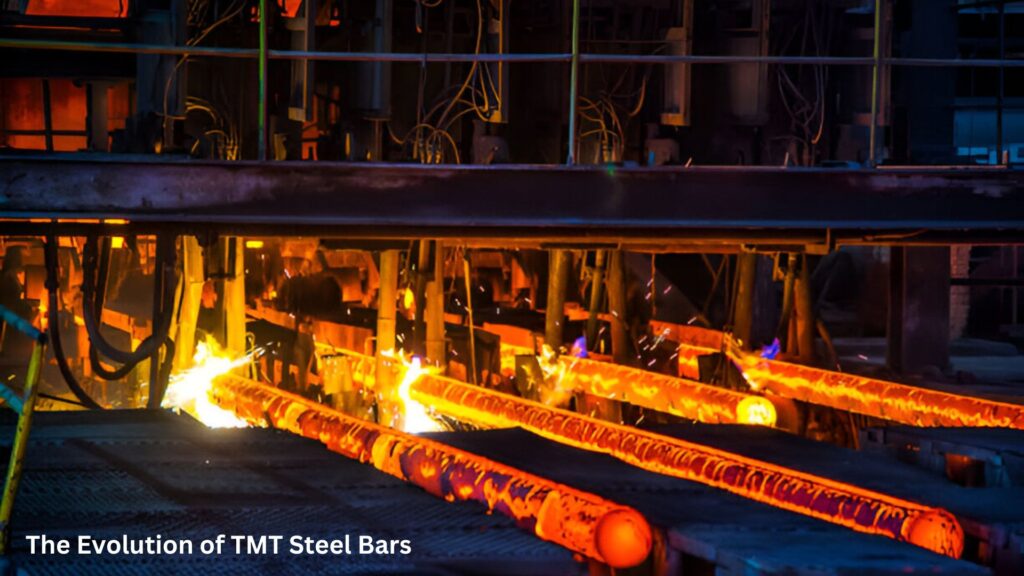
History of TMT Steel Bars
TMT steel bars have a rich history dating back to the mid-20th century when the concept of reinforcing concrete structures gained prominence. Traditional steel bars, often referred to as mild steel bars, were widely used for their strength and durability. However, these bars had limitations in terms of ductility and corrosion resistance, prompting the development of alternative solutions.
Advancements in TMT Manufacturing
The evolution of TMT steel bars began with the introduction of thermo-mechanical treatment (TMT) in the manufacturing process. This revolutionary technique involved subjecting the bars to controlled heating and cooling cycles, resulting in superior mechanical properties and enhanced performance. TMT bars offered higher strength, improved ductility, and better corrosion resistance compared to traditional bars, setting a new standard in construction reinforcement.
Controlled Heating and Cooling
The TMT process involves three stages: quenching, self-tempering, and atmospheric cooling. During quenching, the hot rolled steel bars are rapidly cooled with water, leading to the formation of a hard outer surface. This is followed by self-tempering, where the core of the bar remains hot and tempers the outer surface, giving the bar a tough and ductile core. Finally, atmospheric cooling ensures the bars achieve the desired strength and ductility.
Enhanced Mechanical Properties
The result of the TMT process is a steel bar that combines high strength with excellent ductility. According to the Bureau of Indian Standards (BIS), TMT bars must have a minimum yield strength of 500 to 600 MPa, making them significantly stronger than traditional mild steel bars. This combination of properties ensures that TMT bars can absorb and dissipate energy during seismic events, making them ideal for use in earthquake-prone regions.
Innovations in TMT Manufacturing
In recent years, advancements in metallurgy and manufacturing technology have further propelled the evolution of TMT steel bars. Advanced techniques such as controlled rolling, quenching, and tempering have become standard practices in TMT bar production, ensuring uniform properties and consistent quality. These innovations have enabled TMT bars to meet the ever-increasing demands of modern construction projects, including high-rise buildings, bridges, and infrastructure.
Controlled Rolling
Controlled rolling involves the precise control of temperature and deformation during the rolling process. This technique enhances the microstructure of the steel, resulting in improved strength and ductility. By optimizing the rolling process, manufacturers can produce TMT bars with consistent properties and superior performance.
Nano-materials and Composite Reinforcement
Emerging technologies such as nano-materials and composite reinforcement are poised to revolutionize the construction industry. Nano-materials can be incorporated into the steel matrix to enhance its mechanical properties, while composite reinforcement involves the use of multiple materials to achieve a synergistic effect. These advancements hold the promise of even stronger and more durable TMT bars, opening up new possibilities for safer and more sustainable construction solutions.
The Future of TMT Steel Bars
Looking ahead, the future of TMT steel bars holds even greater promise as researchers and manufacturers continue to push the boundaries of innovation. Emerging technologies such as nano-materials, composite reinforcement, and smart construction are poised to revolutionize the construction industry, offering new possibilities for safer, more sustainable, and more efficient building solutions. TMT bars will undoubtedly play a central role in these advancements, providing the foundation for the buildings of tomorrow.
Smart Construction
The integration of smart construction techniques, including the use of sensors and data analytics, can enhance the performance and durability of TMT bars. By monitoring the structural health of buildings in real-time, smart construction can identify potential issues before they become critical, ensuring the safety and longevity of the structure.
Sustainable Practices
Sustainability is a key focus in the future of TMT steel bar manufacturing. The use of recycled steel in the production of TMT bars reduces the environmental impact and conserves natural resources. Additionally, advancements in energy-efficient manufacturing processes and waste management techniques contribute to the overall sustainability of TMT bars.
Government Initiatives
The Government of India has introduced various initiatives to promote the use of sustainable construction materials. The Steel Scrap Recycling Policy, introduced by the Ministry of Steel, aims to enhance the availability of scrap steel for recycling, reducing the dependence on imported raw materials and promoting self-reliance. Such initiatives support the growth and development of the TMT steel bar industry, ensuring a sustainable and resilient future.
The evolution of TMT steel bars from traditional to advanced manufacturing techniques is a testament to human ingenuity and progress. From their humble origins to their current status as indispensable components in modern construction, TMT bars have come a long way. With ongoing advancements and innovations, TMT steel bars will continue to shape the future of construction, ensuring safety, sustainability, and structural integrity in every project.
At Rama TMT, we are proud to contribute to the construction of safer and more resilient high-rise buildings, shaping skylines and safeguarding communities for generations to come.